Virtual trade show
|
Automation
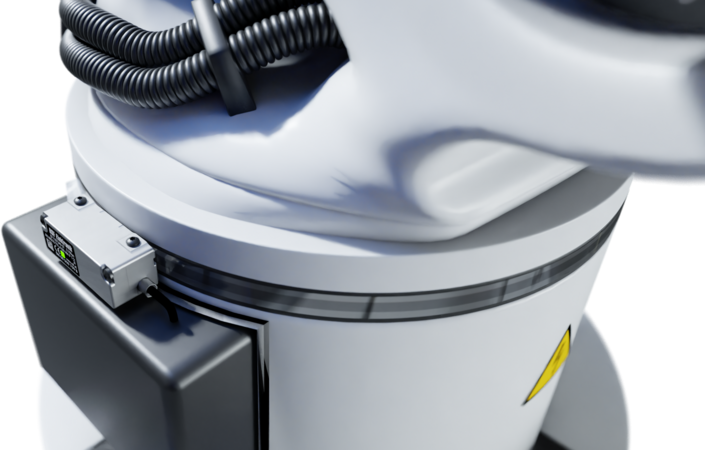
More solutions with special features
Their special characteristics make them ideal for robotics: explore the many robot-suitable encoders and system solutions from HEIDENHAIN and its brands AMO, LTN, NUMERIK JENA, RENCO, and RSF. These include a rotary encoder for press-fit mounting on small motors, as well as the EnDat 3 interface with bus operation, enabling the integration of multiple encoders within your system. Find out more about these and other exciting products and technologies:
The new inductive PressFit rotary encoders
Rotary encoders with bearing shield
The ultra-flat RENCO rotary encoders
Maximum flexibility with encoders from RSF
Intelligent system integration with EnDat
Exposed encoders for high dynamic performance
The KCI 419 Dplus rotary encoder for elevators
LTN slip rings in robotics applications